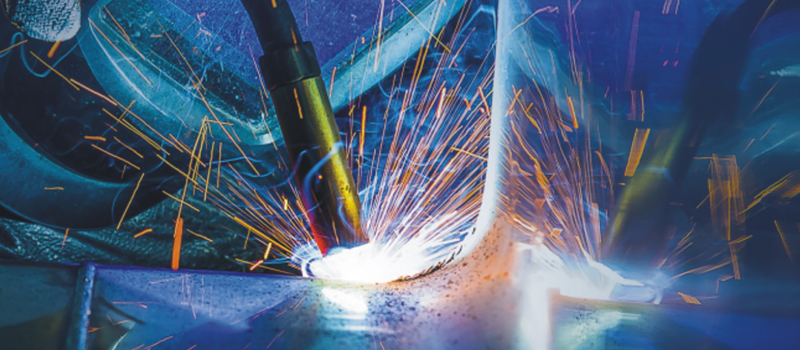

The core system of the welding robot of the future is self-learning
Add Date:2023/6/15 Views: 152
Its self-regulating properties are based on a new sensor system controlled by a neural network program. In most cases, monitoring sensors are used during welding, which track the bevel angle, an important part of the welding process. In the system developed by, there are also monitoring sensors for the heat distribution (heat value of the weld pool) and the form of the weld. The monitoring data is transmitted from the sensors to the neural network, which is able to infer and react to simultaneous changes in several variables.
'When an error is detected, the system is able to correct it during the welding process and calculate any other faults that may occur. Thus, the end result is a flawless product. The problem with welding automation systems is that certain values are set for the job, the entire weld is performed based on that value and then the result is checked for goodness. Now, the entire process is monitored for welding
In the gas shielded arc welding process, factors that affect the quality of the result include the welding current, the arc voltage, the wire feed and delivery speed and the position of the welding torch. With the help of neural networks, adjustment windows can be set for these system variables, which can then be controlled to keep them within limits, thus ensuring that the end product meets the requirements.
"In practice, this means that when the weld value approaches the boundary value set in the parameter window, the system corrects the process so that the weld value moves back towards the temperature range and prevents possible defects."
Adding value to Arctic steel construction
The new system is suitable for welding high-strength steel, as the parameter window for high-strength materials is significantly narrower than for construction steel, and the harder the steel, the more difficult it is to weld. An example is the use of high-strength steel in Arctic steelwork, where the materials used are light, strong and robust.
"In the Arctic, the quality of welding is higher than in warmer regions. In the north, mistakes can have disastrous consequences. For example, welds can withstand temperatures of up to -60°C and are operated with a very high degree of insurance against any accidents.
The markets for the new system developed are worldwide. The system can be used for example in the manufacture and quality verification of pressure vessels, different types of vessels, pipes and piping systems, booms and beam structures. The welding industry has been waiting for such a control system since automatic welding entered the market.
The system will bring significant savings to the welding industry as resources will no longer be required for post-weld inspection and maintenance. However, the system can only be used for large-scale welding operations, so manual welding will continue to be used for a variety of jobs that cannot be performed by robotic welders.
'When an error is detected, the system is able to correct it during the welding process and calculate any other faults that may occur. Thus, the end result is a flawless product. The problem with welding automation systems is that certain values are set for the job, the entire weld is performed based on that value and then the result is checked for goodness. Now, the entire process is monitored for welding
In the gas shielded arc welding process, factors that affect the quality of the result include the welding current, the arc voltage, the wire feed and delivery speed and the position of the welding torch. With the help of neural networks, adjustment windows can be set for these system variables, which can then be controlled to keep them within limits, thus ensuring that the end product meets the requirements.
"In practice, this means that when the weld value approaches the boundary value set in the parameter window, the system corrects the process so that the weld value moves back towards the temperature range and prevents possible defects."
Adding value to Arctic steel construction
The new system is suitable for welding high-strength steel, as the parameter window for high-strength materials is significantly narrower than for construction steel, and the harder the steel, the more difficult it is to weld. An example is the use of high-strength steel in Arctic steelwork, where the materials used are light, strong and robust.
"In the Arctic, the quality of welding is higher than in warmer regions. In the north, mistakes can have disastrous consequences. For example, welds can withstand temperatures of up to -60°C and are operated with a very high degree of insurance against any accidents.
The markets for the new system developed are worldwide. The system can be used for example in the manufacture and quality verification of pressure vessels, different types of vessels, pipes and piping systems, booms and beam structures. The welding industry has been waiting for such a control system since automatic welding entered the market.
The system will bring significant savings to the welding industry as resources will no longer be required for post-weld inspection and maintenance. However, the system can only be used for large-scale welding operations, so manual welding will continue to be used for a variety of jobs that cannot be performed by robotic welders.